Imagine the limited aspirations of the first
pre-bronze age constructor to join two pieces of wood with a sharp implement.
History does not record who it was, but the incredible results
of that inspirational moment are all around us - in the houses we live in, the bridges we
cross, the furniture we sit on.
Nails have been around for a long time. As soon as man
discovered that heating iron ore could form metal, the ideas for shaping it quickly
followed.
Wrought handmade nails (Wrought =
beaten into shape by hammer blows)
In the UK, early evidence of large scale nail making comes from
Roman times 2000 years ago. Any sizeable Roman fortress would have its 'fabrica'
or workshop where the blacksmiths would fashion the metal items needed by the army. They
left behind 7 tons of nails at the fortress of Inchtuthil in Perthshire.
For nail making, iron ore was heated with carbon to form a dense
spongy mass of metal which was then fashioned into the shape of square rods and left to
cool. The metal produced was wrought iron. After re-heating the rod in a forge, the
blacksmith would cut off a nail length and hammer all four sides of the softened end to
form a point. Then the nail maker would insert the hot nail into a hole in a nail header
or anvil and with four glancing blows of the hammer would form the rosehead (a shallow
pyramid shape).

An original 7" (180mm) long Roman nail found in Scotland
This shape of nail had the benefit of four sharp edges on the
shank which cut deep into timber and the tapered shank provided friction down its full
length. The wood fibres would often swell if damp and bind round the nail making an
extremely strong fixing.
In Tudor times, we have evidence that the nail shape had not
changed at all as can be seen by the nails found preserved in a barrel of tar on board the
'Mary Rose' - the Tudor flag ship of Henry VIII built in 1509 and recovered from the mud
of the Solent in 1982.
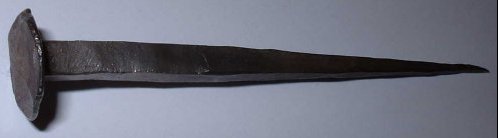
A replica of the hand made nails found on board the 'Mary Rose'
Machine made nails
It was not until around 1600 that the first machine for
making nails appeared, but that tended really to automate much of the blacksmith's job.
The 'Oliver' - a kind of work-bench, equipped with a pair of treadle operated hammers -
provided a mechanism for beating the metal into various shapes but the nails were still
made one at a time.
Eventually, in the USA, towards the late 1700's and early
1800's, a nail machine was devised which helped to automate the process. This machine had
essentially three parts. Flat metal strips of around two feet (600mm) in length and the
width slightly larger than the nail length was presented to the machine. The first lever
cut a triangular strip of metal giving the desired width of the nail, the second lever
held the nail in place while the third lever formed the head. The strip of metal was then
turned through 180° to cut the next equal and opposite nail shape off the strip. These
nails are known as cut nails.
Because the nail up until then was handmade, the first machines
were naturally designed to re-produce the same shape of product - a square tapered nail
with a rosehead, but only tapered down two sides of the shank.
Soon nail making really took off, primarily in the USA and also
the UK with its captive markets of the British Empire. The cut nail was produced in large
numbers and various other shapes were devised to suit different purposes.
In the heartlands of the industrial revolution, many nail
factories had row upon row of these nail machines and the incessant clatter from them
created a deafening sound.
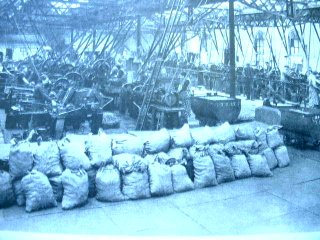
This old photograph from the early 1900's shows a typical nail shop -
notice the machines are pulley driven
But still, the process was labour intensive with a man (or
woman) attending each machine.
By the start of the 1900's, the first coils of steel round wire
were produced and quickly machines were designed to use this new raw material. The first
automatically produced wire nails with no human intervention other than to set up the
machine immediately showed that this was the way to produce a cheaper nail.
The fact that the nail had a round parallel shank that had up to
four times less holding power didn't matter so much. Thinner timbers were being used in
construction and other forms of fastening were becoming available if a strong fixing was
needed.
The wire nail quickly became the nail of choice as it is today
because of its price and the cut nail's day was numbered.
In the 21st century, the nail making process through the ages is
now being used by the restoration industry to help to establish when a building was built.
Hand made nails suggest the building was built before 1800. Cut nails suggest the building
was built between 1800 and the early 1900's. Wire nails will be found in a building put up
in the period from then to date.
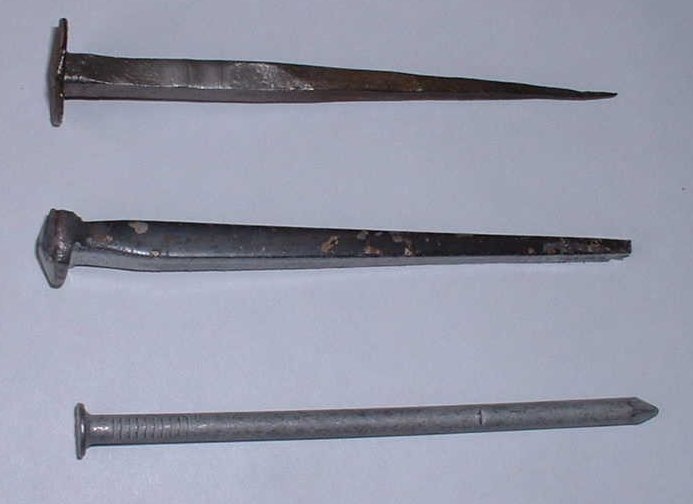
Hand made nail (top) Cut nail (middle) Wire nail (bottom)
Restoration
There is currently an enormous interest in preserving our
heritage and much of that heritage is in the shape of the buildings that remain as
evidence of a bygone age.
For the restorer, it is vital that the correct raw materials are
used in any attempt to preserve an old building. Nails are no exception. The restorer is
looking to use similar nails to ensure the authenticity of the restored building.
While it is possible to get a blacksmith today to produce a
handmade nail from wrought iron, the cost can be prohibitive and the blacksmith is not
keen to devote his limited time to making such small products.
However, almost a century after their predicted demise, there
are still two cut nail manufacturers worldwide in existence employing the process that is
almost 200 years old and using machines that have barely changed in design in that time.
One such company is Glasgow Steel Nail Co which can trace its
business roots back to 1870. In addition to working with these old machines, the
process also involves preserving the blacksmith's skills to form cutting and heading
tools.
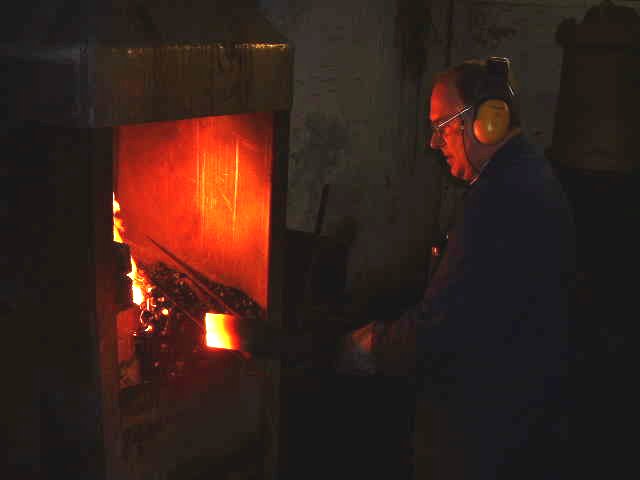
A new cutting tool is removed from the smiddy fire
As explained earlier, the first cut nail machines replicated the
handmade nail - the square tapered nail with a rosehead. Because the process still
involves a man (or woman) presenting a strip of metal to a machine, the resulting nail is
necessarily imprecise - that is each nail can look a little different to the next one.
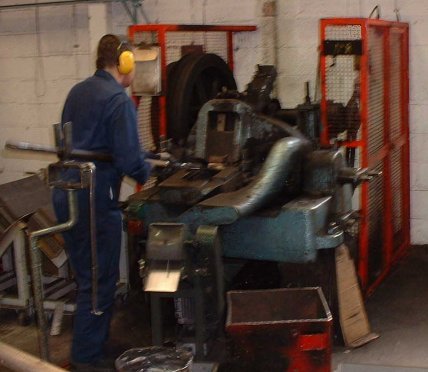
A view of a cut nail machine today - notice the ear protection!
Click here to watch a movie
of the process
The result is that these cut nails are often mistaken for
handmade nails. In use, the rosehead is often the only part of the nail that is left
visible and this shape of head is now considered vital when a period nail is demanded.
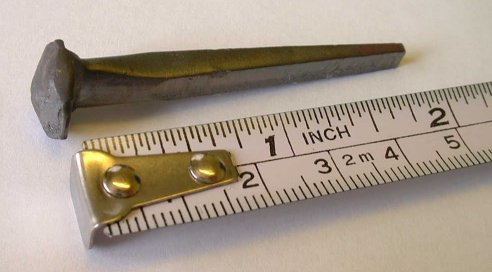
A Décor nail used mainly for studding on doors
Whether the project involves restoration or the building of a
replica, a genuine cut nail made using a process that has not changed in 200 years lends a
degree of authenticity to the project.
The nails are normally made of mild steel and are often used
without any further finish and can be clinched (i.e. bent over by 90° to lock the nail in
place). A recent expensive project involved nails for studding on large outside doors
which would be deliberately left to rust to provide greater authenticity. Nails can also
be produced in copper and bronze.
Glasgow Steel Nail Co has been involved in many interesting projects that have included providing nails for the Globe Theatre
in London, restoration work on Stirling Castle and other castles. The nails are generally
used for doors, floors, gates, indeed anywhere a period nail has to be displayed. The
company is also prepared to consider special projects, for example, it produced a bronze
boat nail for the building of the replica ship the 'Matthew' that in the year 2000
re-traced the 500 year old voyage of John Cabot who discovered New Foundland.

The bronze nail specially made for the 'Matthew'
Traditional cut nails worth preserving?
Over the years, the cut nail has faced the problem of
competition with its rival the wire nail and its history as the first common nail.
One aspect of that has been the expectation that because wire
nails are cheap, the cut nail should also be cheap. After all, it's just a nail.
Attempting to follow that line of thought, no matter how ridiculous as the processes are
so different, has meant that many cut nail manufacturers have ceased business over the
years because margins were so low.
The process is as much part of our heritage as the products
produced and it will be necessary for those involved in the restoration industry to change
the mindset of trying to compare cut nail and wire nail prices, if the process is to
survive.
One way of changing the mindset is to think in terms of the
price per nail in comparison with other old artifacts being used and indeed what can be
purchased today. Cut nails for the restoration industry can amount to just a few pence
each and it only takes a moment to assess their long term value say in comparison with the
can of Coca Cola or Mars Bar you might buy for lunch.
A recognition of the value cut nails offer is needed to ensure
that the process is not lost for ever and encourage the handing on of the skills involved.
Indeed, the price is not dissimilar to that charged for hand wrought nails in medieval times.
You can read in more detail
about the early nail trade in the UK if you click here.
You can read another article
on the history of nail making if you click
here.
For even more detailed
information on nail chronology to help determine the age of a building; the shapes of hand
made nails; the first cut nails which were then headed in a second process; the fight
during the period 1790-1820 to be the first to design the best 'one process' cut nail
machine; or you would like to look at the British Army's Nail Standards manual dated 1813,
here are the sources for these articles particularly the ones noted below.
Lee H. Nelson: Nail
Chronology As An Aid to Dating Old Buildings, Technical Leaflet 48. Nashville: American Association for State and
Local History, 1968,
Maureen K. Phillips: Mechanic
Geniuses and Duckies, A Revision of New England's Cut Nail Chronology Before 1820,
APT Bulletin Vol. XXV No. 3-4, and Mechanic Geniuses and Duckies Redux: Nail Makers
and Their Machines, APT Bulletin XXVII No. 1-2. Association for Preservation Technology
International